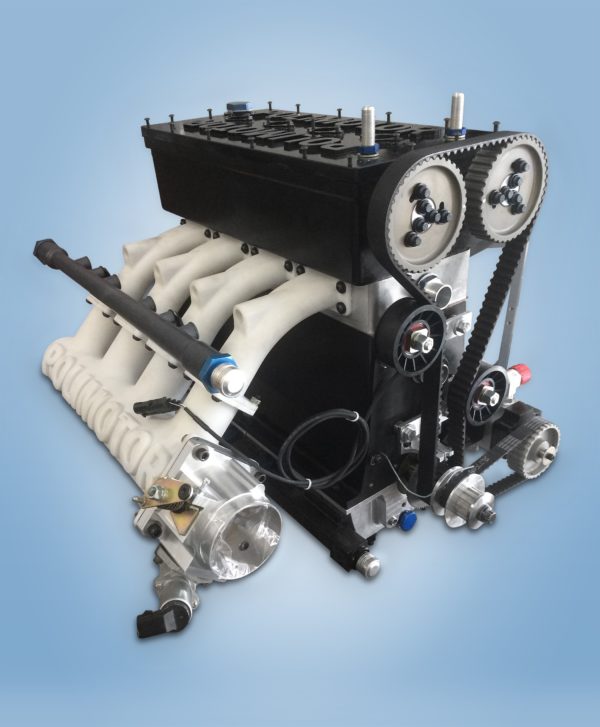
All the power…
without the weight
161 Pounds!
Polimotor 3D (P3D) uses carbon fiber and 3D printing of the composite and metal parts, so it is now 16 pounds lighter than the Polimotor 3, and is 10 BHP more powerful thanks to the OBR engine management system. In 2020, a normally aspirated P3D will power a sports prototype in the FARA USA series in Homestead, Florida. In 2021, a turbocharged P3D may return to hillclimbing and possibly Pikes Peak.
– PURE SUPER LIGHTWEIGHT RACING ENGINES –
HISTORY
In 1972, Matti Holtzberg established Polimotor Research to develop fiber reinforced polymers that could be used to replace metal parts in internal combustion engines. Ahead of its time in 1980, he successfully created Polimotor 1, the world’s first polymer engine. Holtzberg designed and developed the Polimotor based on a Ford 2000cc engine with cast iron block. His polymer design weighed just 180 lbs., about half the weight of the metal engine, and produced 280 BHP at 8500 RPM.
In 1985, Holtzberg shocked the global automotive industry and motorsports world by successfully competing in the IMSA Camel GT Championship and later in the Gulf Oil British Hillclimb series where it “blitzed massive 2 liter opposition” by beating the top 2 liter racing engines in the UK and Europe with what was essentially the World’s first polymer racing engine.
In response to the growing demand for lighter and more fuel-efficient cars from global automakers, Holtzberg took his design to the next level and created Polimotor 2 and 3, using his latest fiber reinforced polymer materials for manufacturing engine blocks. The Polimotor 2’s polymer engine block, oil pan, cam box, and cam cover are molded using a fiber-reinforced thermoset molding compound and a molding process developed by Holtzberg. The Polimotor 2/3 block weighs 6 Kg less than Ford’s latest Ecoboost 2.0 aluminum block.
Today the World’s first polymer engine is rapidly becoming the World’s first 3D printed metal and polymer engine using both 3D printed polymer parts as well as 3D printed metal parts. The camshafts are 3D printed in Inconel 718 and DLC coated and the 3D printed aluminum cylinder bores have a proprietary coating on the bores. The next metal parts to be 3D printed are the titanium valves, steel tappets, titanium con rods (aluminum for hillclimbs) and a super light hollow, steel crankshaft. The latest dry sump oil pan design will be 3D printed using a carbon fiber thermoplastic.
FEATURED NEWS
Polimotor Destroys 2 Liter Competition in UK Hillclimbs
The original Polimotor won four prestigious hillclimb competitions in the UK. Here's what the press had to say... "Polimotor blitzes massive 2 liter opposition" "Scott Young bags his first Gulf Oil...
Polimotor 2 project targets all-plastic engine for competitive racing
Reprinted from Plastics Today - July 2016 Injection-molded oil pump housing to employ PAEK polymer Led by legendary automotive innovator Matti Holtzberg, the Polimotor 2 project aims to design and...
Littlestar Plastics Talks About The Polimotor 2
In the world of polymers, Matti Holtzberg is a legend – and Littlestar Plastics is honored to be a part of his latest push to bring the automotive industry into the 21st century with his Polimotor...
Permatex Partners with Polimotor to Build Engines of The Future
Posted on: December 21st, 2017 – Permatex Sealants and Gasket Makers used in revolutionary polymer engine – Permatex®, a leading innovator in chemical technology for automotive maintenance and...
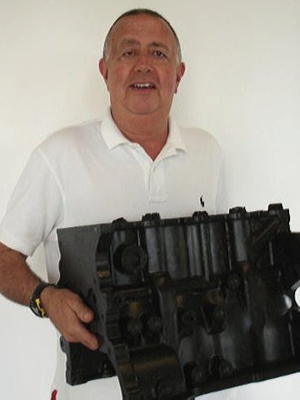
Matti Holtzberg
Polimotor LLC
Wellington, Florida
908.963.4652
matti@polimotor.com